The Single Strategy To Use For Large Double Glazed Glass Panels
Table of ContentsWhat Does Insulated Glazing Panels Do?What Does Glazing Infill Panels Mean?Glazed Window Panels Things To Know Before You Buy
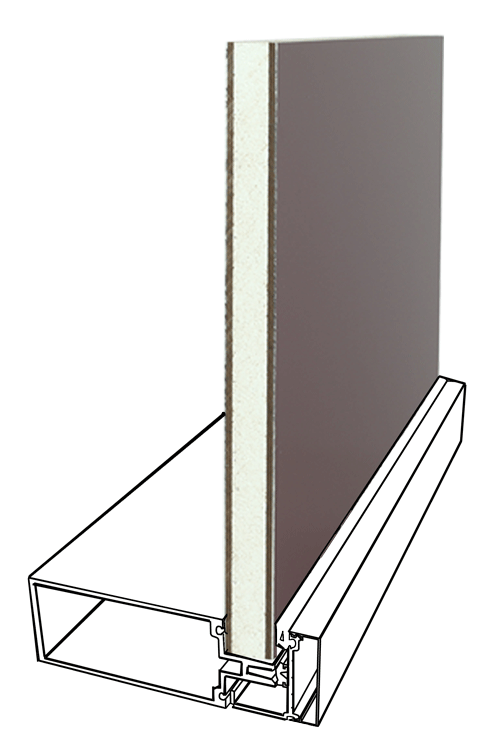
The service life span of parts that are mated with the curtain wall into an assembly should match the service life span of the curtain wall itself. Require resilient flashing materials, non-corroding attachment hardware and fasteners, and wetness resistant products in areas subject to wetting. Lab testing: For tasks with a substantial amount of custom curtain wall, require laboratory testing of a mock-up curtain wall prior to settling job shop drawings.
Specify that laboratory tests are to be performed at an AAMA Accredited Lab facility. Field Mock-up: For all curtain walls, stock or customized, need construction and testing of a field mock-up agent of the wall/window assembly. This is best scheduled prior to the release of store illustrations for window production, so that there is a chance to make style modifications based on the test efficiency of the field mock-up.
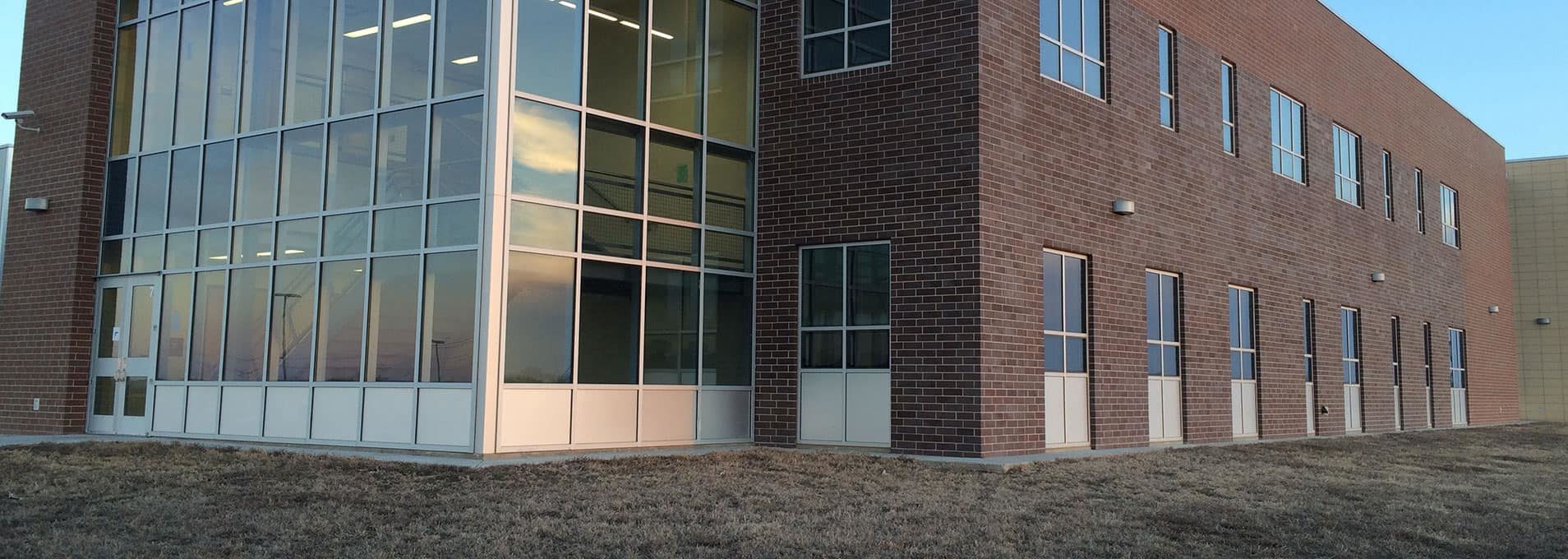
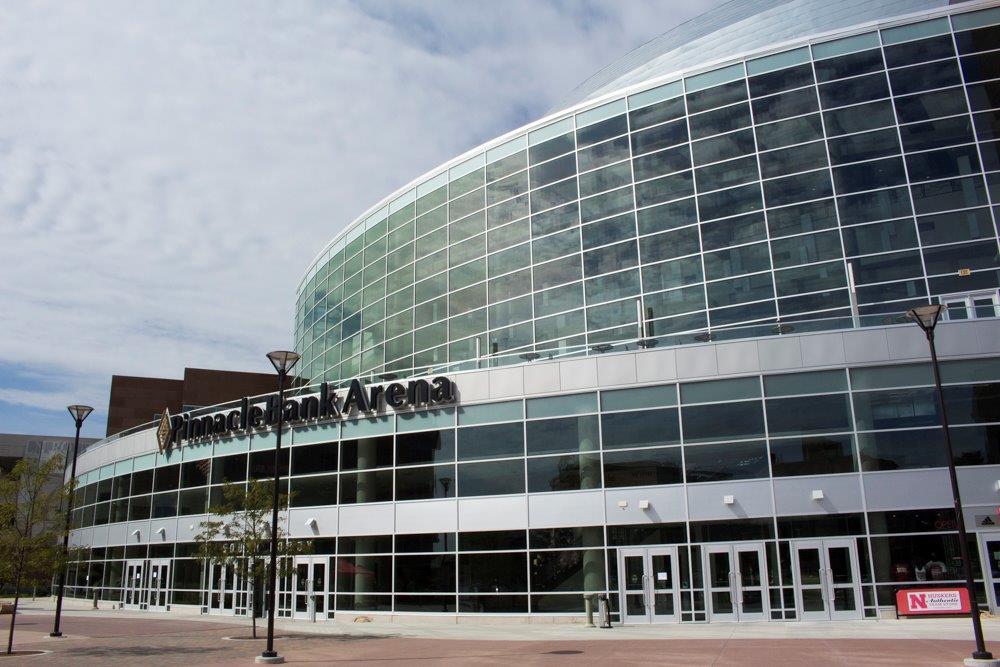
Field screening of drape walls: Require the field testing of drape walls for air infiltration and water penetration resistance, for quality control of drape wall fabrication and installation. Need numerous tests with the first test on preliminary installations and later tests at approximately 35%, 70% and at last completion to catch problems early and to validate continued workmanship quality - glazed panel window.
Shop drawing coordination: Require drape wall installation shop illustrations showing all surrounding building and associated work, including flashings, accessories, interior finishes, and showing sequencing of the work. Drape wall systems, especially unitized systems, require expertise on the part of the building designer, the manufacturer, the producer, and the installer. For all however the easiest of systems, the designer must consider engaging an outside specialist, if such proficiency is not offered on the personnel.
The Ultimate Guide To Fire Rated Glass Vision Panels
The details connected with this section of the BEDG on the WBDG were established by committee and are meant solely as a method to show basic style and building ideas only. Suitable use and application of the principles showed in these information will differ based upon efficiency factors to consider and environmental conditions special to each project and, for that reason, do not represent the final viewpoint or recommendation of the author of each section or the committee members responsible for the advancement of the WBDG.
Elevation consists of splice joints to accommodate thermal motion of the drape wall frame. A through-wall metal flashing at the base of the brick cladding above the curtain wall safeguards the drape wall from leakage through the wall above (see Outside Wall) for combination of the these parts. Locate Your Domain Name outside perimeter sealant joints behind trim cover to prevent water inside trim cover from bypassing the exterior sealant joint.
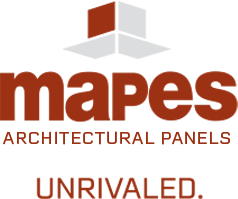
Locate setting blocks as to not block water drain from the glazing pocket. Supply anti-walk blocks at the jambs of the glazing units. Blocks must be gapped 1/8-inch from the edge of the glazing unit. Note: the following U-series details are courtesy of The Facade Group This elevation shows a normal unitized drape wall assembly hung from the edge of the flooring slab.
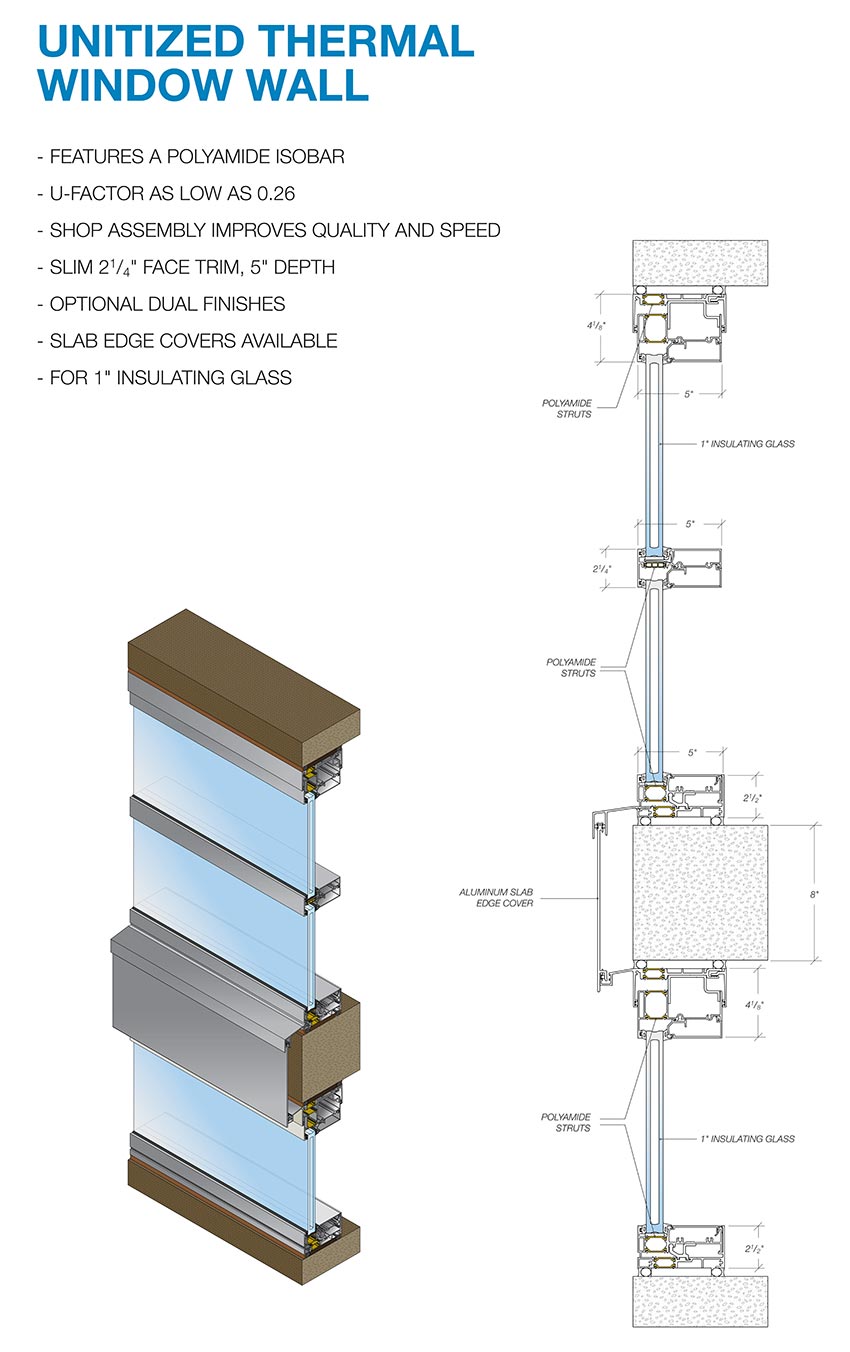
Glazed Spandrel Panel Things To Know Before You Get This
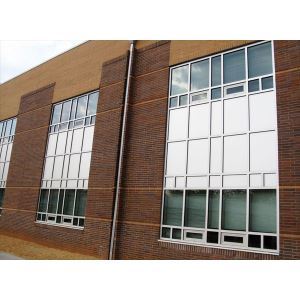
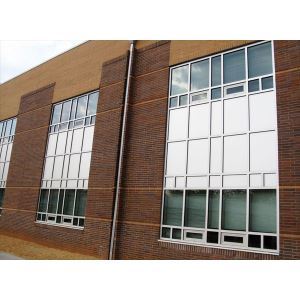

Spandrel glass adapters are utilized to minimize the depth of the glazing pocket to accommodate lowered profile of spandrel glass. Spandrel glass adapters must be fully bedded in sealant and incorporated with glazing pocket corner seals to prevent water leak from glazing pocket to building interior. System measurement of breeding head and sill extruded profiles permits specified flooring to floor deflection at the stack joint.